|
|
|
|
|
|
|
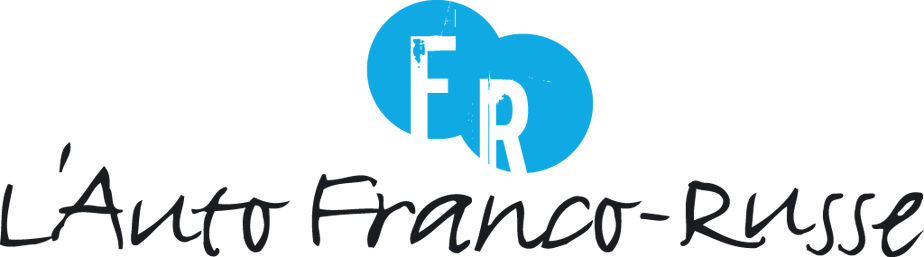 |
|
|
|
|
|
|
|
France-Russia Automotive |
|
|
|
|
|
N° 11
June
2011 |
|
 |
Price :
10 € TTC |
|
|
Français
English
Russian |
|
|
|
|
|
|
France-Russia Automotive
(Auto Franco-Russe) is an economic newsletter focusing on the
development of the Western automotive groups’ business in Russia.
France-Russia Automotive is distributed both on paper and electronically.
To receive the next issues for a free trial you only need to
subscribe on our
website: www.autofrancorusse.fr.
France-Russia Automotive is
published by
Agence du Fil SARL Company,
whose publications are devoted to the Franco-Russian trade. |
|
|
|
|
|
|
|
|
|
|
|
|
|
|
In this issue |
|
|
|
|
|
|
|
|
|
The Russian car market is recovering faster than
expected. With 1.235 million cars and commercial vehicles sold in the
first six months of 2011, over course of the year the market could reach
a value close to that of before the crisis. Several car manufacturers
have confirmed their desire to increase their presence in Russia,
signing new assembly agreements with the State.
Ford and VW are developing projects to raise their on-site production
capacity to over 300,000 units each. Renault is preparing for the
assembly of its models at Avtovaz, its local partner. Still with weak
market presence, Fiat also intends to establish an assembly plant there.
The tyre manufacturers are not lagging behind: Pirelli and Continental
plan to set up factories in Russia.
The manufacturers are come together with local parts manufacturers to
aid their modernisation. |
|
|
|
|
The Editor |
|
|
|
|
|
|
|
|
EVENT |
|
|
|
|
|
|
|
|
CONTINENTAL AND
PIRELLI HAVE DECIDED TO SET UP IN RUSSIA |
|
|
|
|
|
|
Continental presented its
planned factory in Kaluga, while Pirelli is currently preparing an
acquisition. |
|
|
|
|
|
|
|
Pirelli plans to establish itself in Russia, probably
by acquiring one or two existing factories. Meanwhile, Continental plans
to build its own factory. The two Western companies are expected to join
Michelin and Nokian which have been present for a long time in Russia,
along with Yokohama which is currently completing the construction of
its factory in Lipetsk, with the start of production scheduled for late
2011.
Continental has just announced plans to build a tyre factory in Kaluga.
Production should begin in 2013 for a capacity of 4 million tyres per
year, with the option to increase it to 12 million. The manufacturer is
going to invest up to 240 million Euros in this project. On this
occasion, Continental has also agreed to sever the joint venture which
links it to Sibur RT, as part of the Matador-Omskshina factory. It was
the Russian partner who requested the break, "so as not to be hindered
by anti-monopoly regulations within the framework of its future
operations with Pirelli", according to its statements. Sibur RT should
buy back the 50% owned by Continental. The factory produced almost 2.8
million tyres in 2010.
According to sources, Pirelli is interested in tyre factories in
Voronezh and Kirov. Both sites belonged to local tyre manufacturer Amtel,
which disappeared during the crisis. The factories fell into the lap of
the local Sibur Russian Tyres, which does not wish to keep them, itself
pending restructuring.
The hypothesis most often proposed would involve the creation of a joint
venture (JV) between Pirelli and Sibur RT, or even several joint
ventures. With the possible involvement of Rosstekhnologii, the Russian
public holding company responsible for managing the industrial holdings
of the State, an agreement to this effect could soon be signed. For now
Pirelli withholds its response, continuing negotiations on the capital
composition of future structures.
So is the emergence of new Western players good news for local or
foreign suppliers of the local tyre industry? Not everyone thinks so.
"The Pirelli project is bad news for us because they will bring their
traditional suppliers, just as Michelin and Nokian have done.
Traditionally, for their establishments around the world, the buying
decisions are made by the parent company, there are no competing
suppliers on-site", states Vladimir Ulicky, head of sales at
Konstrukta, a Slovak company producing equipment for the tyre industry.
The Russian market represents 5% of its current turnover.
"The local tyre manufacturers haven't been able to break into this"
"The local tyre manufacturers have not succeeded in their transition.
In their independent approaches, Sibur, Amtel and others, have competed
with each other. The result is that they could not get past it",
says Anton Iablonitsky, member of the board of directors of VIPO, a
Slovak company specialising in the engineering of equipment for the tyre
industry. A supplier of Sibur since 2000, VIPO also worked for the Kirov
factory, the two factories in Voronezh, the Matador-Omskshina factory
etc.
It does not expect new orders with the arrival of Pirelli and
Continental. "The Western tyre manufacturers are very conservative,
not open to new suppliers. Rubber does not always react in a predictable
manner, unlike steel. There is much empirical evidence, that the
expertise of a tyre manufacturer is an accumulation of its experiences."
The VIPO equipment is however installed in the Voronezh factory, and
likely to fall into the lap of Pirelli, "Yes, we have equipped this
factory even at the time of Vredestein; it was they who had selected our
products," confirms Mr. Iablonitsky.
In addition, the Pirelli proposal with Sibur Russian Tyres challenges
the major project alliance between Sibur RT and Nizhnekamskshina, a
local tyre manufacturer located in Tatarstan. As part of this proposal
under discussion since 2010, the two main local tyre manufacturers were
to place their commercial assets of passenger vehicle tyres and truck
tires in a common pool, managed by the management team of Sibur RT.
Negotiated at the highest level of the Russian State, this project has,
however, been met with resistance. According to local experts, Sibur RT
did not wish to include the factories in Kirov and Voronezh within the
scope of the agreement, preferring to sell them to a western
manufacturer. Nizhnekama did not wish to transfer the all-steel workshop
nor its own research centre. The implementation of this alliance is no
longer on the agenda. "The objective of the project alliance between
Sibur Russian Tyres and Nizhnekamskshina was to create a structure
capable of competing with Bridgestone and Continental in our market. But
if Sibur disperses its assets, this will be bad for us and for all those
involved in the local industry," states Alexander Pichugin, DG of the
national centre for research on tyres "NIISHP Scientific and Technical
Centre". |
|
|
|
back to contents |
|
|
|
|
|
|
|
|
|
|
|
STRATEGIES |
|
|
|
|
|
|
|
|
FIAT
STANDS ALONE |
|
|
|
|
|
|
Abandoned by its local partner,
the Italian manufacturer will set up on the Russian market by itself,
where it can count on political support. |
|
|
|
|
|
|
|
After many setbacks, Fiat has finally signed an
agreement with the Russian state for an assembly plant. The
manufacturer's proposal envisages a capacity of 25,000 units per year.
But the Russian authorities encourage Fiat to increase the project size
to 120,000 units and add to it the construction of an engine factory, so
as not to deviate too much from the conditions they impose on other
Western manufacturers. The Italian manufacturer does not appear hostile
to this invitation, but requests a credit from the state-owned bank
Sberbank for an amount estimated at nearly 1.1 billion dollars from
Russian sources. It will probably make its decision based on the
response of the bank. Any decision to grant a foreign company a credit
of this size based on public funds, will essentially have political
overtones. In the event of refusal, Fiat would take the opportunity to
return to a more modest configuration of its initial proposal.
The Italian manufacturer sets off with a handicap. Its brand is little
known in Russia. Consumers have had time to forget that the full old
range of Lada, still very popular, is a local derivative of the Fiat
124. Dedicated "Car of the Year" in 1967, it was assembled in the USSR
since 1970, and production continues today at Avtovaz and Izhavto. As
for Fiat, the Italian manufacturer has not been able to benefit from the
growth of the automotive market in Russia during the past decade. Sales
under the Fiat brand reached 21,943 cars in 2010, compared with 96,466
units for Renault or 58,989 for VW, according to statistics from the AEB.
This puts Fiat at 19th place in the sales charts for the Russian market.
An attempt to create a joint venture (JV) with local Sollers, had been
negotiated in 2010. This partner had already hatched from its assembly
lines, the Doblo, Linea and Albea models in its factories in Tatarstan.
The project involved the construction of a high capacity factory, for
between 300,000 and 500,000 units per year. The Memorandum of
Understanding (MoU) was signed in the presence of Prime Minister Putin,
who had promised the partners public funding. But just before the final
signature, there was a twist: in February 2011 Sollers announced that it
had broken away from Fiat, preferring an alliance with Ford.
Finding itself without a local partner, Fiat decided to set itself up
alone on the Russian market. But the configuration announced by the
manufacturer, 25,000 cars per year, does not correspond at all to those
imposed today to its competitors. Those who wish to benefit from an
assembly agreement with customs preferences, must submit a proposal for
a minimum of 300,000 cars. Clearly the case of Fiat does not fit here.
An exemption for the Italian manufacturer?
Would the Italian manufacturer have benefited from an exemption? The
local administrative authorities are not unaware of the friendship
displayed by the Russian Prime Minister to his Italian counterpart. And
which results in an interest buoyed by Mr. Putin in proposals from major
Italian manufacturers like Fiat or the tyre manufacturer Pirelli. The
unusual thing is that it was Putin himself who had promised state
funding for the failed Fiat project. A promise that was never revoked.
The manufacturer can expect a friendly attitude on the part of the
administrations. They found a way for Fiat to set up without following
the rule. They took from the archives, a file on an assembly agreement
filed by the local subsidiary of Fiat in 2008, and which had never been
followed. Application filed in 2008, permission granted in 2011, but,
with the conditions prevailing in 2008, therefore a minimum capacity of
25,000 cars per year.
The location of the future factory is not yet known. The Russian sources
advertised Fiat's interest in the region of Nizhny close to the GAZ
automobile cluster but without a direct link with this local
manufacturer, already committed to GM. Fiat has not confirmed anything
for the moment. The manufacturer intends to assemble vehicles there
under its own brand, as well as models of Jeep, little known in Russia
today. The exact configuration is likely to depend on the possibility of
finding the necessary funding. The Italian manufacturer has to catch up
with the Russian market, but not at any price. |
|
|
|
back to contents |
|
|
|
|
|
|
|
|
|
|
|
VW AND GM
ASSEMBLE UNDER CONTRACT AT GAZ |
|
|
|
|
|
|
VW and the GAZ Group signed an agreement to bring about the
assembly of VW and Skoda models in the local manufacturer's factory in Nizhny.
Finalised in June 2011, the project includes the assembly of the Skoda Octavia
and Skoda Yeti, and the VW Jetta, from late 2012. The goal is to produce 61,000
units in 2013, 88,000 in 2014, and up to 110,000 cars per year from 2015. The
formula chosen by the partners is that of assembly under contract. VW is
investing 115 million Euros in this project, and GAZ, 85 million Euros. This
project complements the production capacity of the factory of the German
manufacturer located in Kaluga, and which can assemble up to 180,000 units.
The local manufacturer is also involved with GM within the framework of an
assembly agreement signed in early 2011. In this context it has been contracted
to assemble 30,000 Chevrolet Aveo from 2012.
The GAZ Group no longer has any model within the passenger sector in its
catalogue since the recent failure of its Siber model, a licensed copy of the
Chrysler Sebring. The project was halted in 2010. It cost the group up to 240
million dollars for the 8,952 cars assembled. Since then, the Sebring assembly
line remains unused. It will be brought back, notably for VW.
The GAZ Group announced a turnover of 3.22 billion dollars for 2010, up 47%
compared to the previous year. Net income reached 70 million dollars, compared
to a 360 million loss in 2009. But the group's growth is always undermined by
the weight of its debt, close to 1.5 billion dollars, and which has not changed
since 2009. GAZ sold 11,061 trucks, 10,818 buses, 82,062 utility vehicles and
nearly 5,000 cars in 2010. The group belongs to the industrial holding company
Russian Machines of the local businessman Oleg Deripaska. |
|
|
|
back to contents |
|
|
|
|
|
|
|
|
|
|
|
RENAULT
SEEKS TO CONTROL THE COSTS OF LOGISTICS |
|
|
|
|
|
|
Are Russian transporters more expensive than their
French counterparts? This is a popular question at Renault. The major
projects of the manufacturer in Russia pose new logistical challenges to
the company. The "localisation" phase of production in its Avtoframos
factory in Moscow, forces it to deal with a growing number of local
suppliers. The localisation rate reached 52% (excluding the powertrain)
in 2010, this being 20 local suppliers for a production of 112,000 cars
per year. "We receive nearly 160 trucks per week in our factory in
Moscow," explained Jean-Philippe Jouandin, director of logistics for
the Renault-Nissan Alliance for Russia. He was speaking on the occasion
of the last Russian Automotive Forum organised by Adam Smith Conferences
in March 2011 in Moscow.
Today, Renault's local suppliers are located in St Petersburg, Yaroslavl,
Nizhny, Vladimir, Togliatti and in the Moscow region. But their
geographical range is likely to expand. In 2011, Renault is expected to
increase production to 200,000 units, with 30 local suppliers and 330
trucks to take delivery of per week. The goal for 2013 is to reach
350,000 vehicles per year with the assembly of Renault models at Avtovaz,
and at least 380,000 including Nissan. The number of local suppliers
would therefore have to rise to 60, for a total of 900 trucks per week.
In anticipation of this growth Renault has launched a program to move
towards ex-works operation, to optimise the total delivery cost.
At the same time the manufacturer is concerned with its own deliveries,
leaving from the factory. Today it needs 700 trucks. In 2013, its needs
will be closer to 1,500 trucks. It is not clear if the transporters are
able to offer it this fleet. And with the gradual entry into operation
of new factories from other car manufacturers, the demand will increase.
In addition, transportation costs have increased quite dramatically in
recent years. From a value of 100 in early 2008 before the crisis, the
costs shrunk to 60 during the crisis, to climb up to 180 in spring 2011.
According to analysis by Renault, the rates offered by local
transporters are now 20% higher than those charged by French operators.
And this annoys Jean-Philippe Jouandin: "The fuel here is cheaper
than in France. The trucks are the same. Salaries and expenses are lower
here than in France. So, I have to ask myself why transportation costs
are now higher than those charged in France. I suggest to the
transporter that it signs a long-term agreement, to regulate the rates.
It replies: OK, but with variable prices! I don't understand it..."
A service provider of Renault, the local operator RTL defends itself by
explaining that it lacks visibility, and this would be the reason for
the rise in prices. In reality, the local transporters operate below
capacity, which causes the increase in rates. Maintaining the shortage
is a way for them to increase margins. Aware of the risks, Renault is
planning its own solutions. "Perhaps an internal structure? Leasing?
All options are open" says Jean-Philippe Jouandin. |
|
|
|
back to contents |
|
|
|
|
|
|
|
|
|
|
|
FORD
EXPANDS INTO TATARSTAN |
|
|
|
|
|
|
Ford has signed an assembly agreement to bring
production to the local company Sollers. United in a joint venture (JV)
the partners are asking the state bank VEB to lend them 1.3 billion
dollars over 10 years, to bring assembly up to more than 300,000 units
per year.
Ford already has a factory in Vsevolozhsk near St Petersburg, which
assembles the Focus, and since 2009, the Mondeo. Nearly 67,000 Focus
cars were sold on the Russian market in 2010. Both models are in demand
on the market. So much so that the factory in Vsevolozhsk recently moved
to the 3x8 work shift system in April 2011. The forecasts are for an
assembly of 90,000 units of both models in 2011, compared with 80,000 in
2010. The maximum capacity advertised for the factory is of 125,000
units, but it has still never been reached.
Sollers has two factories with a capacity of 110,000 and 90,000 units,
located in Tatarstan. It also has an engine factory located in the
region of Nizhny, with a capacity of 250,000 parts per year.
The partnership with Sollers offers Ford an opportunity to better meet
market demand. But above all, the agreement with Sollers allows it to
display a large project, of more than 300,000 units per year, a
condition imposed by the Russian authorities to renew its assembly
agreement with the preferential customs terms, and which expires in
2013. |
|
|
|
back to contents |
|
|
|
|
|
|
|
|
|
|
|
KAMAZ SEEKS SUPPLIERS |
|
|
|
|
|
|
The truck tyre manufacturer is
poised to revitalise its range with models from Western manufacturers,
and it is looking for new suppliers. |
|
|
|
|
|
|
|
KAMAZ has just revised its forecasts for the domestic
market upwards from 14 to 40 tonnes for 2011, bringing it from 72,000
units to 95,000 units. The proportion of vehicles destined for road
freight would be equal to 32% - 33% in these forecasts. The truck tyre
manufacturer, the national market leader, has also revised the forecast
of its own sales upwards, from 30,000 to 38,000 units in this segment.
This market presents new challenges for the local industry. "We
realised that users did not want ox-drawn carts," said Mr. Ashot
Arutyunyan, marketing director of KAMAZ. He was speaking on the occasion
of the last Russian Automotive Forum organised by Adam Smith Conferences
in March 2011 in Moscow. To maintain its market share, KAMAZ pins its
hopes on its project with Daimler, also a shareholder in the Russian
manufacturer: Daimler owns in partnership with the EBRD, a 15% stake in
KAMAZ. The project took the form of a 4x2 vehicle assembled with a large
proportion of components used by Daimler, notably the engine, cooling
system, exhaust, cab, part of the transmissions system. Two units will
be presented at the Comtrans trade fair in Autumn 2011 in Russia.
"This vehicle will be positioned in the premium low, or middle-high
segments. According to our survey, nearly 20% of users of our trucks
will be interested in this new model", adds Mr. Arutyunyan.
The manufacturer is developing several other projects. The assembly with
Mercedes Benz started in March. The vehicle is positioned on the premium
range, the sales forecasts were 1,100 units in 2011, 2,000 in 2012, and
2,500 in 2013. Another assembly, this time with Mitsubishi Fuso, is for
a 7.5 tonne truck. The sales forecasts were 1,700 units in 2011, 2,500
in 2012, and 3,500 in 2013. This 6-8 tonne segment is considered the
most dynamic on the Russian truck market. KAMAZ has also tried to
propose several "restyled" models for the market, with Daimler, Cummins
and ZF parts. But these models met with a mixed reception from potential
users, because of projected rise in costs that will be at least 15%. The
manufacturer is notably faced with resistance from the Department of
Defence, one of its major public clients. The military do not want to
hear about a vehicle with a German built cab. The company has tried to
build its own cab to meet the demands of "national design", but the
costs of it have doubled in relation to the original.
The production of new models, in particular with Daimler, also means
looking for new suppliers. This is where KAMAZ has some difficulties,
according to Mr. Arutyunyan: "The German partner imposes its own
suppliers on us, but it does not have technical documentation on their
parts and it has no right to send it to us. We must therefore negotiate
with each parts manufacturer. It is a very long negotiation; we make a
proposal and we wait two months for the answer. It may be necessary that
we ourselves find equivalent solutions on-site". |
|
|
|
back to contents |
|
|
|
|
|
|
|
|
|
|
|
MAZ AND KAMAZ: A
DIFFICULT MARRIAGE TO NEGOCIATE |
|
|
|
|
|
|
The proposed acquisition of MAZ, a manufacturer of
trucks located in Belarus, by KAMAZ, its Russian competitor, does not
seem to be moving forward. Announced at the start of the year, this
project is still at the stage of preliminary discussions.
MAZ's capital is held by the Belarusian State, which grants it financial
guarantees on orders for export. As part of the discussion, it was
envisaged that KAMAZ would receive 100% of MAZ's capital and in
exchange, the Belarusian party would receive a yet-to-be-defined share
of KAMAZ's capital. It is the definition of this part that is
problematic. The commercial relationship between the Russian companies
and the Belarusian manufacturers in the public arena, is often
complicated because of the tumultuous political relationship between the
two countries. On the other hand, Daimler holds an 11% stake in KAMAZ
and the partners are in negotiation regarding several joint ventures
based around Mercedes-Benz, which might require an increase in the share
of German manufacturer. The European bank, EBRD, also holds 4% of the
capital of KAMAZ; its share is managed by Daimler.
MAZ assembled up to 20,000 units before the crisis, mainly trucks and
some buses. The Russian market is its main client, absorbing nearly 65%
of its production for trucks. The Belarusian company had sold nearly
3,000 trucks in Russia in the first quarter of 2011, according to its
statements.
KAMAZ realised 32,300 units in 2010, compared with 26,000 in 2009. Its
sales would be raised to nearly 7,000 trucks in the first trimester of
2011. The capital of the company is held by the public holding company
Rosstekhnologii (49.9%), the investment bank Troika Dialog (27.3%) and
by Daimler and the EBRD (15%). |
|
|
|
back to contents |
|
|
|
|
|
|
|
|
|
|
|
THE CITY OF MOSCOW
HESITATES OVER THE EXIT OF THE ZIL FACTORY |
|
|
|
|
|
|
The City of Moscow, the principal shareholder of the
ZIL automobile factory, has failed to decide on the future of the
company, hesitating between closure and keeping it on "life support". A
specialist in trucks, the oldest Russian automobile factory has been
virtually bankrupt for several years, accumulating a debt of nearly 500
million dollars, for a turnover of 82 million dollars in 2010, and
losses of 9 million dollars over the same period. Configured to produce
up to 200,000 vehicles, the factory assembled 2,260 units in 2009 and
only 1,260 in 2010, mainly 3 tonne and 7.5 tonne trucks. In the first
quarter of 2011 its turnover totalled 12 million dollars with losses
close to 17 million dollars. The rental of surfaces in disused buildings
and the sale of land are still the most profitable activities as they
bring ZIL up to 30 million dollars per year.
The company has thus been loss-making for several years, kept afloat by
the City of Moscow, concerned with preserving political appearances and
not announcing the closure of this industrial site located near the
centre of Moscow. However, since the arrival of Serguei Sobianine, the
new Mayor of the capital since Autumn 2010, things seem to be moving. In
the Spring of 2011 Mr. Sobianine dismissed the management team of ZIL,
after accusing them of misappropriating much of the subsidies granted by
the City. However, no legal proceedings have been instituted yet. The
Mayor hesitated as to the continued operation of the struggling factory.
Some of ZIL’s land could be transferred to developers with their eye on
its 275 ha alongside the Moskva River. But the city also wants to
maintain on-site car production, and seeks partnerships in this
perspective. However, the debt burden and the state of the land polluted
by nearly a century of industrial use, make any project uncertain. |
|
|
|
back to contents |
|
|
|
|
|
|
|
|
|
|
|
LOGISTICS EXPERT GEFCO
SERVES PSA AND VW |
|
|
|
|
|
|
GEFCO, the PSA transporter delivered nearly 7,000
containers in 2010 to the manufacturer's factory in Kaluga, from the PSA
site in Vesoul in France. The rail route now runs at a rate of one train
per day. The passage from partial assembly (SKD) to full assembly (CKD)
caused an increase in shipments, from 330 containers to 70 containers
per week. Some of the deliveries to the Kaluga site come from Japan,
intended for Mitsubishi which shares the site with PSA.
GEFCO also offers its services to other manufacturers in Russia. It
operates in particular for the VW group, also established in Kaluga. The
French logistics expert is responsible for the transport of imported
vehicles from the port of St Petersburg, the removal of those assembled
in Kaluga and their distribution across Moscow and St Petersburg. The VW
network consists of 241 dealers. Its warehouse in Pushkino near Moscow
allows the manufacturer to ensure same day delivery to Moscow and next
day delivery to St. Petersburg. |
|
|
|
back to contents |
|
|
|
|
|
|
|
|
|
|
|
TESTIMONY |
|
|
|
|
|
|
|
|
"The status of the
special economic zone allows us to have fewer problems than elsewhere".» |
|
|
|
|
|
|
Explanations of Andrei Aliev,
Regional Sales Manager at Bekaert Wires LLC, a Belgian manufacturer of
tyre casing which opened its factory in the "economic zone" of Lipetsk
in the South of Russia. |
|
|
|
|
|
|
|
France-Russia Automotive: Why choose Lipetsk for
the establishment of the factory?
Andrei Aliev: The choice of Lipetsk is that of a "special economic
zone", so we benefit from tax advantages, plus the benefits granted by
the regional administrative authorities, including those regarding
infrastructure, connections to electricity grids and gas etc. And above
all, we have fewer difficulties than other actors elsewhere.
The proximity of the Novolipetsk steel plant is advantageous in HR
terms, because in the area there are a lot of employees available, well
trained in production. As for the transportation of our products, it is
easily done by truck as there is a dense road.
- Who are your competitors on the Russian market?
- The Uralkord factory, the SeverstalMetiz factory in Orel, and the BMZ
factory in Belarus. Other producers such as Magnitka fail to ensure a
minimum quality, so their products are not in demand.
- Who are the clients of Bekaert in Russia?
- All of the tyre manufacturers present here, except Michelin. All are
equipped with Steelastic machines, to cover the rubber cables. Michelin
is supplied elsewhere. Nokian in Vsevolozhsk is an example of a good
client. They are increasing their production capacity and implementing
new production lines.
- Are you in contact with Yokohama, which is establishing itself in
your region?
- We are in discussion with Yokohama. They will begin production in a
few months. For now they have planned workforces above what is
necessary, as they intend to gradually implement all stages of the
production cycle, including the mixing, and increase future production
capacity. |
|
|
|
back to contentss |
|
|
|
|
|
|
|
|
|
|
|
 |
|
|
|
|
|
|
|
|
|
|
MARKETS |
|
|
|
|
|
|
|
|
THE NEW GROWTH OF THE
RUSSIAN MARKET |
|
|
|
|
|
|
With 1,235,442 cars and utility vehicles sold on the
Russian market in the first six months of 2011, the market is regaining
its strength just as before the crisis. According to statistics compiled
by the Association of European Businesses (AEB)in Russia, the market had
jumped 56%, in relation to the first six months of 2010, while in 2010,
the sales of cars and utility vehicles had already shown a 30% increase
for 2009.
Continuing this trend, the market could reach 2.5 to 2.7 million units
over the year - almost the same level as before the crisis, when it
reached 2.7 million in 2008. Note that this growth is higher than the
forecasts of analysts. The firm PriceWaterhouse did not foresee a return
to that level before 2014. "With these results, we find that the
Russian market has fully stabilised," says David Thomas, director of
the Automobile Manufacturers Committee of the AEB and also president of
Volvo Car Russia.
At the top there is the local brand Lada Avtovaz which sold 291,540 cars
during the first six months of 2011, or 31% more than during the same
period in 2010. Chevrolet sold 81,527 units which is 54% more than in
the same period of 2010. And Renault sold 74,337 units, at an increase
of 76%.
Among the brands that have displayed the best growth, Nissan sold 59,374
units, an increase of 119% over the same period in 2010; VW sold 45,517
units, an increase of 102%; and Mitsubishi sold 35 006 units, an
increase of 135%. |
|
|
|
|
|
|
|
Learn more about the AEB |
|
|
|
|
|
|
|
The Automobile Manufacturers Committee of the
Association of European Businesses in Russia publishes the monthly
statistics for sales of cars and commercial vehicles, of all
manufacturers, Western and local, operating on Russian territory.
Without distinction, the statistics cover the sales of new vehicles
assembled on-site or imported.
www.aebrus.ru |
|
|
|
back to contents |
|
|
|
|
|
|
|
|
|
|
|
THE RUSSIAN PARTS
MANUFACTURING MARKET: COMPLICATED AND DIFFERENT FROM OTHER COUNTRIES |
|
|
|
|
|
|
Improving quality at a local parts
manufacturer is a Herculean task. Yet the demand for locally
manufactured parts is strong. This market is promising. |
|
|
|
|
|
|
|
With the large plans of car manufacturers in Russia,
finding parts manufacturers at proximity is a critical issue. How does
one find reliable suppliers? The topic is regularly discussed at the
Russian Automotive Forum conferences organised by Adam Smith Conferences
in Moscow. Those who have tried to supply themselves using local parts
manufacturers, often provide disappointed testimony. Some quotes:
"Of the 300 Russian parts manufacturers, less than 30 meet our
requirements" (VW).
"It's easier to bring international suppliers than to develop
production with local parts manufacturers who have no money"
(Volvo).
"Local suppliers have insufficient knowledge of the automotive
market. Furthermore, they are not reliable, the price may change after
signing, the product quality does not always correspond to the samples"
(Bosch).
"There is no process of industrial organisation among local parts
manufacturers. And the costs are not low. It is more expensive than in
Poland or the Czech Republic but we manufacture on-site because the
customs tariffs are very high" (Faurecia).
However, the market for car parts in Russia presents a sizeable
challenge. It could be close to 28 billion dollars, according to
analysis by the GAZ Group. From which to fuel vocations. But this market
is also different from those of developed countries. "According to
the average in the automotive industry worldwide, almost 70% of car
parts manufactured are intended for assembly (OEM), and 30% for the
aftermarket. In Russia, the ratio is the reverse: 25% of parts are
intended for OEM and 75% for the aftermarket," explains Igor Grun,
CEO of BelMag, a supplier of suspension parts for Lada-Avtovaz. BelMag
posted a turnover of 15.5 million Euros in 2010, for 273 employees. The
strong demand for parts for the aftermarket is attributed to the ranges
Lada Avtovaz cars. These vehicles, of poor quality, represent almost 43%
of the fleet. "How can the Russian car parts market be compared to
that of other countries? The statistics do not mean much..." adds
Igor Grun.
The parts market has suffered from the crisis. But there again, not in
the same way as markets in developed countries. "The market for parts
fell by 23% during the crisis, because the demand for parts as original
equipment fell 40%. Meanwhile, the aftermarket has remained much more
stable. But a significant portion of sales from “grey” imports,
estimated at nearly 72% in 2008", observes Rudy Amirkhanian, a
partner at local consulting firm Strategic Initiatives. According to his
analysis, "Russia is a low-cost country because the cost of labour is
low and the cost of electricity is low. But the prices are often higher
than in other countries because the volume of the market is unstable. As
for local equipment manufacturers, they have no R&D role. Overall their
added value is low". A legacy of the planned economy of Soviet
times, when the manufacturer was responsible for designing all the parts
needed for a future model. And then go back to the manufacture, using
the few parts manufacturers present, much of which were integrated
within their own structures.
Renault inspects its suppliers.
This was notably the case for Renault-Avtovaz, which has now launched an
extensive program of quality improvement and which multiplies the number
of inspections at suppliers. "When we visit the local parts
manufacturers, they tell us: "we are going to show you our
machines!" I answer, "no, we do not want to see your machines...
we want to see what's wrong with your machines!" Just because you
have ISO certification and machinery "Made in Germany" doesn't mean that
you will have quality" jokes Nuno de Morais, director of the new Renault-Avtovaz
joint venture for quality and development of suppliers (Common Supplier
Quality and Supplier Development). Established in Russia since 2008, he
is also responsible for the Lada Quality Plan. He was involved in the
latest Russian Automotive Forum in March 2011 in Moscow.
Renault-Avtovaz has initiated a selective improvement programme for
suppliers, to raise them to an acceptable level of quality. This now
covers 67 parts manufacturers. "We must rethink all the processes at the
supplier, up to the recycling of parts found to be non-compliant.
Otherwise you risk finding the same parts in subsequent deliveries,"
explains Nuno de Morais.
At the same time, the company gradually introduced supplier diversity.
The new model of Avtovaz, the Lada Granta, whose assembly is expected to
begin in late 2011, reflects this trend. Nearly 30% of its components
should come from Western manufacturers. Notably on the list are Bosch,
the Japanese company Takata, Valeo, Visteon, Behr, etc. The rest of the
parts come from local suppliers of the Lada Kalina range, of which the
Granta is an evolution.
The efforts of Renault-Avtovaz in the field of quality aim to reduce the
defect rate in the current Avtovaz models, which the local manufacturer
attributes to the unsatisfactory quality of its parts manufacturers. The
goal for 2010 was to go from the 750 defects ppm usually observed, to
150 defects ppm. This goal was not met, for various reasons. The goal
for 2011 is yet more ambitious: to fall to 80 defects ppm. The French
manufacturer sets the bar high. It fully intends to clear out the
stables of Augeas at Avtovaz, before beginning production of Renault
models there. |
|
|
|
back to contents |
|
|
|
|
|
|
|
|
|
|
|
THE LOCAL TYRE
INDUSTRY STRUGGLES TO EMERGE FROM THE DOLDRUMS |
|
|
|
|
|
|
Old and obsolete equipment, and
the disappearance of whole sectors of the chemical industry, undermine
the local production of tyres. |
|
|
|
|
|
|
|
Participants in the Tyres & Rubber trade fair in
Moscow in March 2011 gave a pessimistic view of the state of their
industry. It suffers from out-dated equipment. "The mixing equipment
for local tyre manufacturers is very old," says Alexander Vorontsov
technical director of Con-Cord Group, representative of Farrel, a
British manufacturer of mixers for the CEI, "The six mixers in the
truck tyre workshop in Nizhnekamskshina date from 1978. They break down
regularly. Not long ago, it was necessary to replace a mixer whose tank
had split. The mixer for the all-steel production line and those of the
workshop for car tyres are operating at full capacity and cannot provide
more. The Sibur RT mixers in Yaroslavl are also very old. Sibur has
started to renew the equipment. There are four remaining to be replaced,
but everything has been stopped because with the change of ownership, we
do not know to whom they should be charged".
Often, the old equipment can no longer meet market demand. This is the
case of the Volzhsky factory within the holding company Sibur Russian
Tyres, and which manufactures textile frames for the needs of the tyre
manufacturer. "The Volzhsky factory produces "raw" casings, not
impregnated and not passed through heat treatment", says a senior
management executive of Sibur RT. "This treatment is carried out
directly by our tyre factories and it prevents us from offering our
casings to other tyre manufacturers, which are used to buying ready-made
products".
Sibur has purchased the equipment needed to install a heat treatment
line, but this equipment is still in its packaging because no one has
thought to construct a building to install this production line.
The weakness of the local chemical industry also poses threats to the
supply of tyre manufacturers. "Many segments of our chemical industry
have disappeared. There is no stability, no medium-term vision",
says Liudmila Shumeiko, manager of the company JULIA, producer and
marketer of resin for tyres. JULIA manufactures its products at the
Uralkhimplast factory in Nizhny Taguil in the Urals. "In my market,
prices of raw materials for my resins have suffered three increases in
two months! They have increased by a total of 20% over this period. This
is due in particular to the closure of three factories among those
making benzol, which fell victim to explosion, fire and bankruptcy. I
suggest to my partner Uralkhimplast that "we set prices and agree to
increase the amount ordered". The partner replied: "it's not
possible! Because the more I produce the more it costs me". Under
these conditions, we would not be able to emerge without government
intervention. But I see no programme to protect local producers..."
The additives industry is endangered
"Additives for the production of tyres represents a small market,
because the equipment used by the Russian tyre manufacturers is often
too old to draw upon some of the perceived benefits of the use of
additives," says Yuri Neklyudov, director of the office of Struktol
which represents the German Schill + Seilacher, specialising in
additives and equipment for quality control of mixtures. "When a
Russian factory buys our additives, it must wait fourteen months for the
customs clearance of its order. These timeframes are very punitive. We
must also pay 15% to 20% in customs duties, plus VAT. And if we want to
send a sample of a value of 3 Euros to one of our customers, we have to
pay up to 300 Euros in miscellaneous expenses... and in the end, the
product does not even reach its destination. Providing our products on
the Russian market is a truly Kafkan journey."
According to the analysis of the NIISHP Scientific and Technical Centre,
the chemical industry known as "low volume chemistry", which
manufactures additives for the tyre, is in poor condition, almost all
companies having gone bankrupt. Only the Cheboksary factory survives.
NIISHP proposed to Victor Khristenko, Minister of Industry and Commerce,
the development of a programme of reestablishment of “low volume
chemistry" on disused military sites, previously engaged in chemical
production. The facilities available on these sites can in part be
reused. According to experts, this "low volume chemistry” is vital,
especially for the production of military tyres and those of aircraft.
“Today it is enough that Western suppliers stop deliveries of
additives, and our tyre production will stop". But policy makers
within the Russian administrative authorities seem to think that the
global market for additives is secured by the presence of Chinese
suppliers capable of compensating for any deficiency in the West.
There have been some success in this segment
Not all suppliers are pessimistic; there are also successes across this
segment. Like that of Pneuform, a Czech company that makes moulds. In
Russia it is represented by Fartop, a local company based in Yaroslavl.
Fartop has a mould maintenance workshop at the Sibur RT factory. Igor
Pomerantzev, Fartop manager, expressed satisfaction: "Pneuform
increased its market share in Russia, we have now nearly 70% of the
market for moulds for the manufacture of car tyres by Russian actors. We
are approached by all local players. Pirelli is asking us to set up a
mould maintenance centre in its future factory in Voronezh. Nokian
sought us to install a maintenance centre in Vsevolozhsk, which would be
responsible for the maintenance of the moulds as well as their
replacement. In the end, Yokohama sought us to equip its future factory
in Lipetsk. Pneuform moulds were shipped to the factory in Japan as a
test and they were used to produce some tyres, with satisfactory
results".
The two market leaders, Sibur Russian Tyres and Nizhnekamskshina
succeeded in launching new products, all-steel tyres for trucks.
Nizhnekamskshina did this in collaboration with Continental. But their
production does not seem to have been a great success so far. "The
all-steel tyres are required in small quantities by the Kamaz factory in
Russia and the truck factory in Minsk, Belarus. They also use imported
products", says Alexandre Nenakhov, research director of Loil
Neftekhim, a multi-brand distributor, tyre industry supplier. "There
is not enough demand for these products. The Kama Steel brand of
Nizhnekamskshina is currently unknown. It will take time to promote it.
Customers are not rushing, not seeing the point because the expected
savings are not very great. The transporters making return trips towards
Europe do not take risks by buying tyres other than those of major
brands. The failure of a tyre occurring in Europe means the involvement
of a break-down service, because a trailer cannot be lifted with the
means on board." The cost of this involvement will outweigh the
savings made on purchasing a set of all-steel tyres, manufactured
locally.
"All-steel tires are still reserved for transporting from
Europe-Moscow, Europe-St Petersburg and Europe-Ekaterinburg. In
addition, deliveries are made via poor quality roads where the all-steel
tyre offers no benefit," states Igor Vesselov, scientific director
of the NIISHP research centre. According to him, "the Chinese tyre
manufacturers seek to gain a share of this market. Their products are
lighter, and less expensive. The Chinese are getting these results by
reducing the number of layers in the tyre. This makes it less solid. For
this reason, many users are reluctant to buy all-steel tyres made in
China". |
|
|
|
back to contents |
|
|
|
|
|
|
|
|
|
|
|
NEWS |
|
|
|
|
|
|
|
|
THE NEW RULES OF ASSEMBLY: IT IS CRUCIAL TO WAIT |
|
|
|
|
|
|
The Russian government has tried to introduce a new
rule for assembly agreements with Western manufacturers. It includes a
commitment by the manufacturer to a minimum production of 300,000
vehicles, the production of body parts and stamping on site, a
production of at least 200,000 engines and transmission systems on site,
and implementation of a research and development centre on site. The
Russian state also requires an investment plan involving a minimum of
one billion dollars. In return, the industry will continue to benefit
from a preferential customs regime for the entry of the necessary
components for its assembly lines.
This is a departure from the rule applied previously, and which included
a commitment to a minimum production of 25,000 vehicles. Most
manufacturers have chosen a configuration of somewhere between 30,000
and 120,000 vehicles per year.
The government has put pressure on the manufacturers already present or
interested, to renegotiate their agreements under the new rule but
without much success. Manufacturers have been reluctant in view of the
size of investment required for uncertain prospects. VW has signed but
does not hide the fact that it plans to invest 115 million Euros and not
a kopeck more. Ford has also signed, asking that the investment is
financed by a Russian state bank. This is one way of saying that it is
the Russians who will pay for the rule that they invented. Renault is
among the beneficiaries of the new agreement, but the French
manufacturer had already fulfilled these conditions, both in the size of
its investment and in the production capacity of its local partner.
Other manufacturers have declined the offer, saying that by the end of
their current contracts, there may be new rules, and that it is crucial
to wait. |
|
|
|
back to contents |
|
|
|
|
|
|
|
|
|
|
|
RENAULT-NISSAN NEGOTIATES THE INCREASE IN ITS STAKE IN AVTOVAZ |
|
|
|
|
|
|
The Renault-Nissan alliance continues discussions
with the public holding company Rosstekhnologii for an increased share
in the capital of Avtovaz. Renault already has a 25% share of the
capital of the Russian company. Rosstekhnologii suggested that the
alliance acquires a further 25% of the capital. The latest news is that
Renault could increase its stake to 35%, and Nissan could account for
15%. Financing is yet to be agreed. Rosstekhnologii is asking for nearly
a billion dollars, equivalent to what Renault had paid for its 25% stake
+ 1 share. Carlos Ghosn does not want to spend more than 415 million
dollars, given the current valuation of the company.
Avtovaz announced a turnover of 4.6 billion dollars for 2010, up 57%
compared to the previous year. Net income rose to 120 million dollars,
compared to a 1.6 billion dollar loss in 2009. The company received
assistance totalling more than 2.5 billion dollars, before and during
the crisis. Avtovaz sold 569,000 cars in 2010, which is 37.5% more than
in 2009. And 236,511 cars have been assembled between January and May
2011, which is 39% more than in the same period of 2010. |
|
|
|
back to contents |
|
|
|
|
|
|
|
|
|
|
|
THE
REFORM OF TECHNICAL INSPECTION HAS COME INTO FORCE |
|
|
|
|
|
|
The Russian Parliament has just reformed the
mechanisms for periodic technical inspection of vehicles. Now the
inspection will be performed by a network of private inspection centres,
to be created on the basis of existing service facilities and dealers,
accredited by the Russian Union of Insurers. In all, about 10,000
control centres should be established by 2012, the date of entry into
force of the new measure. The preliminary passage into one of the
control centres will be required for the issuance of the compulsory
insurance policy for the civil liability of drivers. Until then, the
realisation of periodic technical inspection was carried out by traffic
police within the Ministry for Internal Affairs. This practice was
deemed to be generating massive corruption levels. According to internal
surveys, up to 70% of the 34 million Russian drivers received their
certificate of conformity without ever presenting the vehicle for
inspection, paying an average bribe of 100 to 150 dollars. |
|
|
|
back to contents |
|
|
|
|
|
|
|
|
|
|
|
LAMBORGHINI WITHDRAWS |
|
|
|
|
|
|
The Mercury dealer specialising in luxury car brands
has just stopped distributing Lamborghinis. Sales of this brand do not
cover the costs incurred by the distributor according to Mercury. It
sold 10 Lamborghini in 2010. Among its other brands, Bentley is the most
popular with 129 units sold in 2010, as well as 66 Maserati and 32
Ferrari. The Mercury Group is the operator of several luxury brands
outside of the car industry: Giorgio Armani, Chopard etc. It also owns
the department store Tsum in central Moscow, where cars are displayed
alongside other luxury brands. The company belongs to local businessmen
and Leonid Strounine and Leonid Fridland. The turnover of the group was
estimated at between 500 and 600 million Euros in 2009. |
|
|
|
back to contents |
|
|
|
|
|
|
|
|
|
|
|
THEFTS HAUNT THE
RUSSIAN AUTOMOTIVE INDUSTRY |
|
|
|
|
|
|
Thefts committed by company staff haunt the Russian
automotive industry. The scale of the damage varies among companies. At
Ford in Vsevolozhsk, three attempted thefts were intercepted in 2010.
The amount of the loot recovered amounted to nearly 600 dollars. At
Avtovaz, known for the high penetration of its business by organised
crime, the department for internal security in collaboration with the
services on the ground observe several cases of large-scale theft each
year. They just caught an internal criminal association practising the
misappropriation of cars during deliveries to dealers. Losses recorded
amounted to almost 33 million dollars for the year 2009 alone. |
|
|
|
back to contents |
|
|
|
|
|
|
|
|
|
|
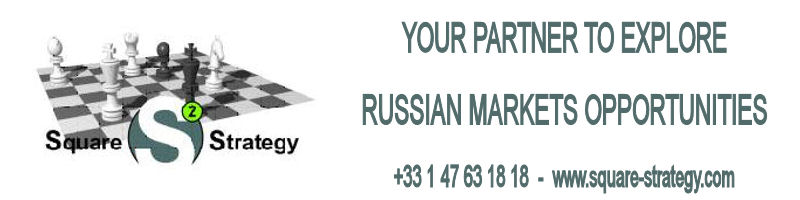 |
|
|
|
|
|
|
|
|
|
|
IN BRIEF |
|
|
|
|
|
|
|
|
The Nissan factory in the suburbs of St.
Petersburg has assembled 17,000 cars in the first six months of 2011.
The site has been operational since 2009 and its advertised capacity is
of 50,000 units per year.
The Russian state has sold its 13.11% share of the capital of the UAZ
factory, which is part of the Sollers group.
Mazda will establish an assembly plant in the Primorye region
located in the Far East of Russia, bordering the Pacific Ocean. The site
will have an assembly capacity of up to 50,000 units per year.
The Izhavto factory resumed service after a long break following
its bankruptcy in 2009. The numbers have doubled since the beginning of
2011; today the factory employs 4,700 people to assemble the old
Avtovaz models.
The Mitsubishi i-MIEV has just been put on sale by the Rolf
dealer network. This is the first electric car to have obtained
certification for the Russian market. It is priced starting at 60,000
dollars. Rolf plans to develop a network of 28 charging stations. |
|
|
|
back to contents |
|
|
|
|
|
|
|
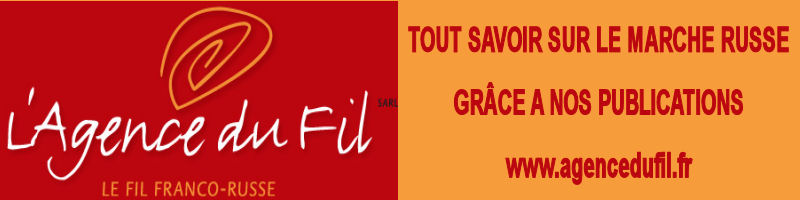 |
|
|
|
|
|
|
|
|
AGENDA |
|
|
|
|
|
|
|
|
Automechanika : from 24 to
27 August 2011 at Moscow
Automotive equipment, car accessories and vehicle maintenance.
mims.ru |
|
|
|
|
|
|
|
Comtrans 2011 : from 13 to 17 September 2011
at Moscow the International Exhibition for Commercial
Vehicles
comtrans.auto-fairs.com |
|
|
|
|
|
|
|
Autoretail Russia 2011 Forum
: from 11 to 13 October 2011 at Moscow
Organised by the Adam Smith Institute, the event will bring together top
executives from both vehicle manufacturers and leading dealerships.
www.adamsmithconferences.com/en/automotive-retail-russia |
|
|
|
|
|
|
|
Russian Automotive Forum : March 2012 at Moscow
An international conference organised by the Adam Smith Institute.
Interventions are planned from the main players from the local and
international industry. You can meat the cream of the leaders in Russian
automobile industry and their purchasing directors.
www.adamsmithconferences.com |
|
|
|
|
|
|
|
Tyre and Rubber Expo: from 16 to 19 April 2012, at
the Expocenter in Moscow Over 200 manufacturers will introduce
their range of tyres for all types of vehicle, rubber parts for the
automotive industry, raw materials and components for the tyre industry,
as well as the parts for production, recapping, balancing etc. The
organisers are expecting 7,000 trade visitors.
www.rubber-expo.ru |
|
|
|
back to contents |
|
|
|
|
|
|
|
|
|
|
|
|
|
|
|
|
|
To
receive the next issues of the France-Russia Automotive/Auto Franco-Russe,
fill the subscription form :
www.autofrancorusse.fr |
|
|
|
|
|
The France-Russia
Automotive is published by the
Agence du Fil SARL Company.
RCS Paris 487 788 051. |
|
|
La maquette de l'Auto Franco-Russe
a été réalisée avec le concours de
l'agence Vingt-Quatre Graphisme |
|
|
|
|
|
|